The electronics industry is rapidly evolving to keep pace with the demands of the modern digital era. As electronic devices become increasingly sophisticated and compact, effective thermal management has become pivotal for optimal performance and longevity. Thermal management ensures that electronic components maintain safe operating temperatures and withstand the intense heat generated, especially in high-power devices. With the miniaturization of circuits and the complexity of component integration, traditional cooling methods are proving insufficient. This calls for advanced thermal management utilizing state-of-the-art heating solutions to take electronics into the future.
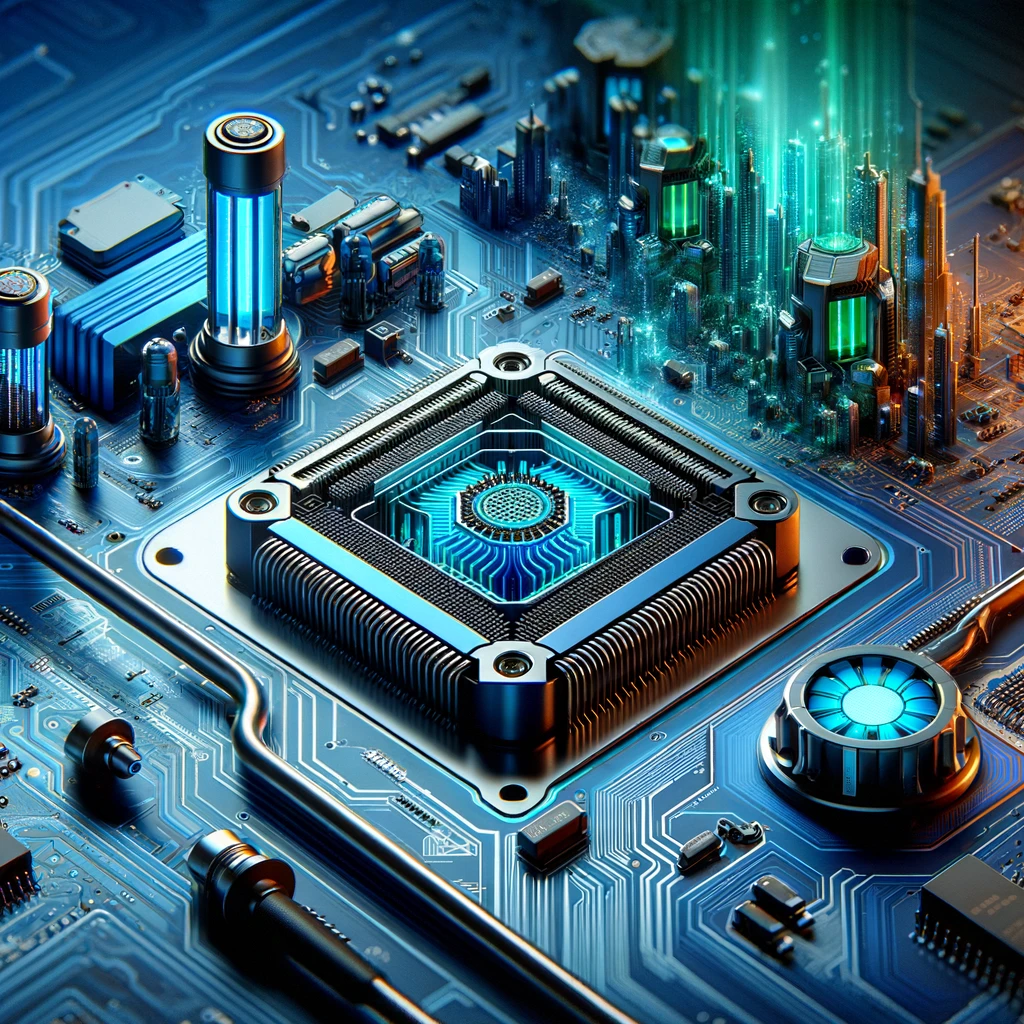
Innovative heater technologies will be integral in revolutionizing thermal control in next-generation electronics. As electronic circuits and systems continue getting denser and smaller, packing more computing power and capabilities, they generate excessive heat flux during operation. If unchecked, overheating causes performance throttling, device failure, system crashes and even safety hazards. Advanced micro-heaters and nanotechnology-enabled heating solutions offer unparalleled efficiency in heat generation, distribution and dissipation. Strategic integration of such technologies will optimize the thermal profiles of electronic components and prevent overheating.
With the electronics sector poised for exponential growth over the coming years, thermal management is fundamental for enabling further breakthroughs. Advanced heaters will be a game-changer in taking electronics into an era of unprecedented innovation – with transformative applications across consumer devices, automotive systems, aerospace, robotics, IoT and more. This new phase will be defined by cutting-edge heating systems overcoming critical thermal challenges and unlocking the true potential of electronic circuits.
Exploring the Role of Heaters in Modern Circuit Design
Heaters are an integral yet often overlooked component in modern electronic circuit design. Their primary role is to provide controlled, localized heating to maintain optimal thermal conditions for sensitive electronic components and systems. Heaters counteract the effects of overheating by dissipating the excessive heat generated during operation. They also preemptively regulate temperatures – a critical function as electronic devices become more complex and compact.
Strategically placed micro-heaters help stabilize the temperatures of processors, sensor modules, power amplifiers, laser diodes and other heat-sensitive components in a circuit. This prevents detrimental thermal expansion, leakage currents and even complete breakdown due to overheating. For instance, flexible polymer heaters are commonly integrated with wearable devices and compact IoT systems to regulate skin contact temperature.
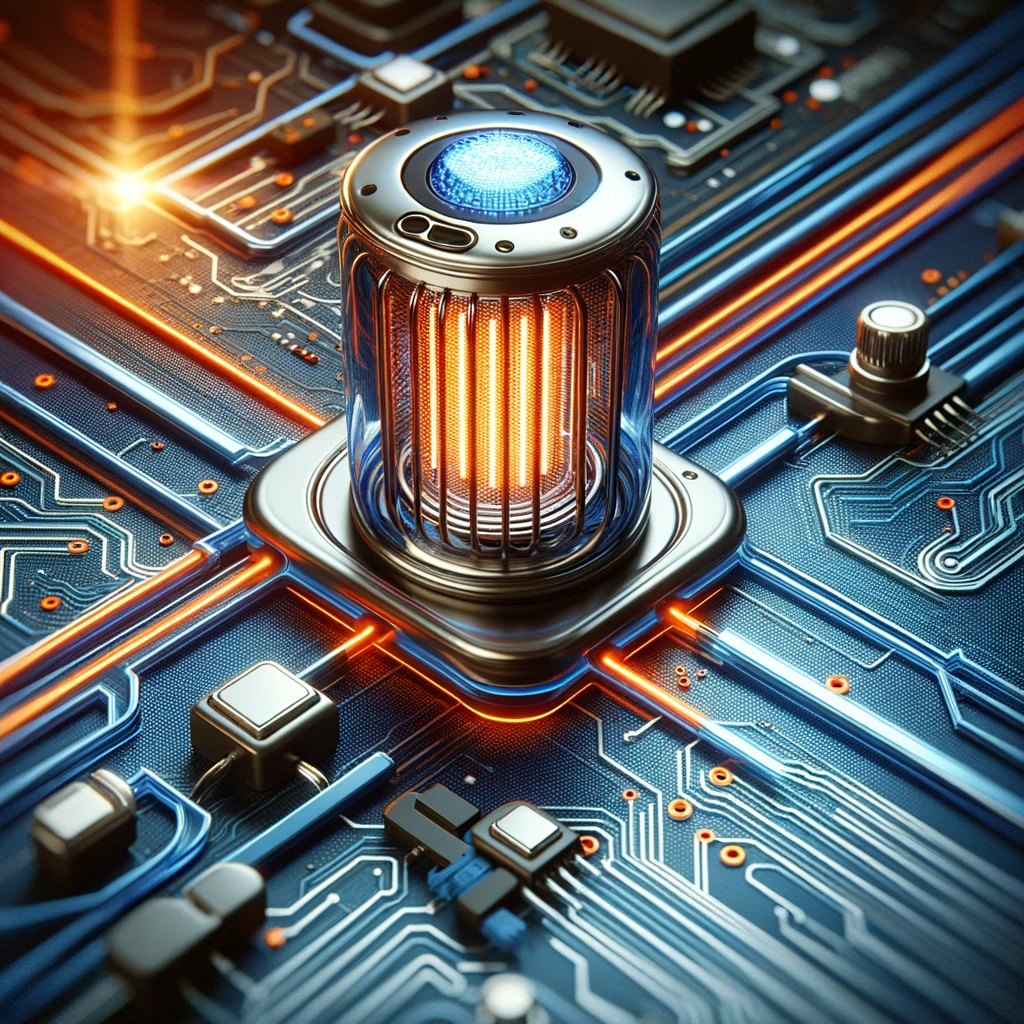
The advanced thermal solutions market offers a wide range of specialty heaters engineered for electronics. These include ceramic PTC heaters, etched foil heaters, silicone rubber heaters, flexible graphite sheets, and other innovative technologies tailored for circuit architectures. Materials with high thermal conductivity like graphene and carbon nanotubes are also gaining prominence in heater design.
Heaters enhance the reliability and longevity of electronic circuits by optimizing heat distribution. This allows components to perform at their peak operating capacity for longer durations. With electronics getting more compact and mission-critical, heaters are becoming essential for thermal management and continued device functionality.
From Basics to Breakthroughs: A Journey in Electronic Thermal Management
The field of thermal management in electronics has undergone tremendous innovation, transforming from rudimentary cooling methods to highly advanced heating solutions. Early electronic devices relied on simple metal chassis, heat sinks and fans for heat dissipation. However, the electronics revolution and the rise of solid-state devices demanded more sophisticated temperature control.
Thermoelectric coolers, cold plates and heat pipes improved heat transfer in 1960s transistors and microchips. Phase change materials, synthetic diamond heat spreaders and liquid immersion cooling were introduced in the 80s and 90s respectively. While these methods aimed at removing heat from electronics, the industry also realized the importance of strategically adding heat to optimize thermal profiles.
The 2000s saw major strides with piezoelectric coolers, microchannel heat exchangers and the advent of thermal interface materials (TIMs) like thermal grease. As circuits shrank in size, micro-fabricated heaters emerged for localized temperature control. Innovations continue today with advanced technologies like self-regulating ceramic PTC heaters, thin-film flexible heaters and nanoengineered thermoelectric modules.
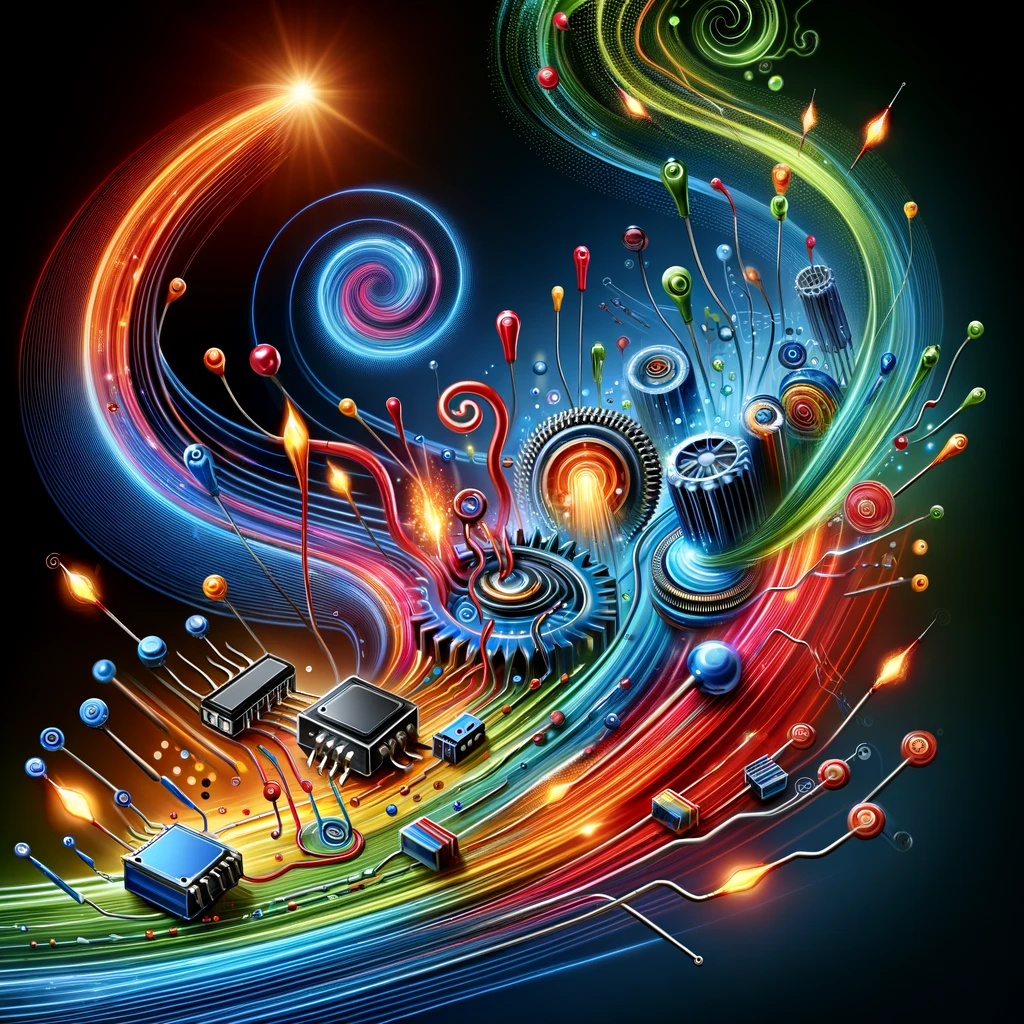
Current research focuses on active heating systems driven by the Internet of Things (IoT), artificial intelligence (AI) and smart materials to dynamically respond to thermal loads. Electronics thermal management is poised to achieve new levels of intelligence, efficiency and sophistication that seemed unfathomable just decades ago. This field will remain seminal for electronics to keep pace with rapid technological developments.
Understanding Thermal Challenges in Electronic Circuits
The intense and concentrated heat generation in modern electronic circuits poses major design challenges. With increased power densities from component miniaturization, thermal management has become critical. Heat-induced failures account for over 55% of all electronic equipment breakdowns. Key thermal challenges include:
Hotspots – Localized overheating due to high power densities in chips/modules leading to performance throttling and reduced reliability.
Thermal expansion – Different expansion coefficients cause mechanical stress like PCB warpage and cracked joints.
Electromigration – Heat effects causing conductor material transport leading to open/short circuits.
Leakage currents – Increased free charge carriers in semiconductors leading to current leakage and power loss.
Thermal shock – Sudden temperature changes causing cracks/fractures in components and solder joints.
Thermal resistance – Stacked interfaces impede heat flow, exacerbating temperature rise.
Ventilation constraints – Compact architectures limiting conventional airflow cooling.
Harsh ambient conditions – Extreme environments aggravating heat accumulation.
User risks – Hot external surfaces causing discomfort/injury.
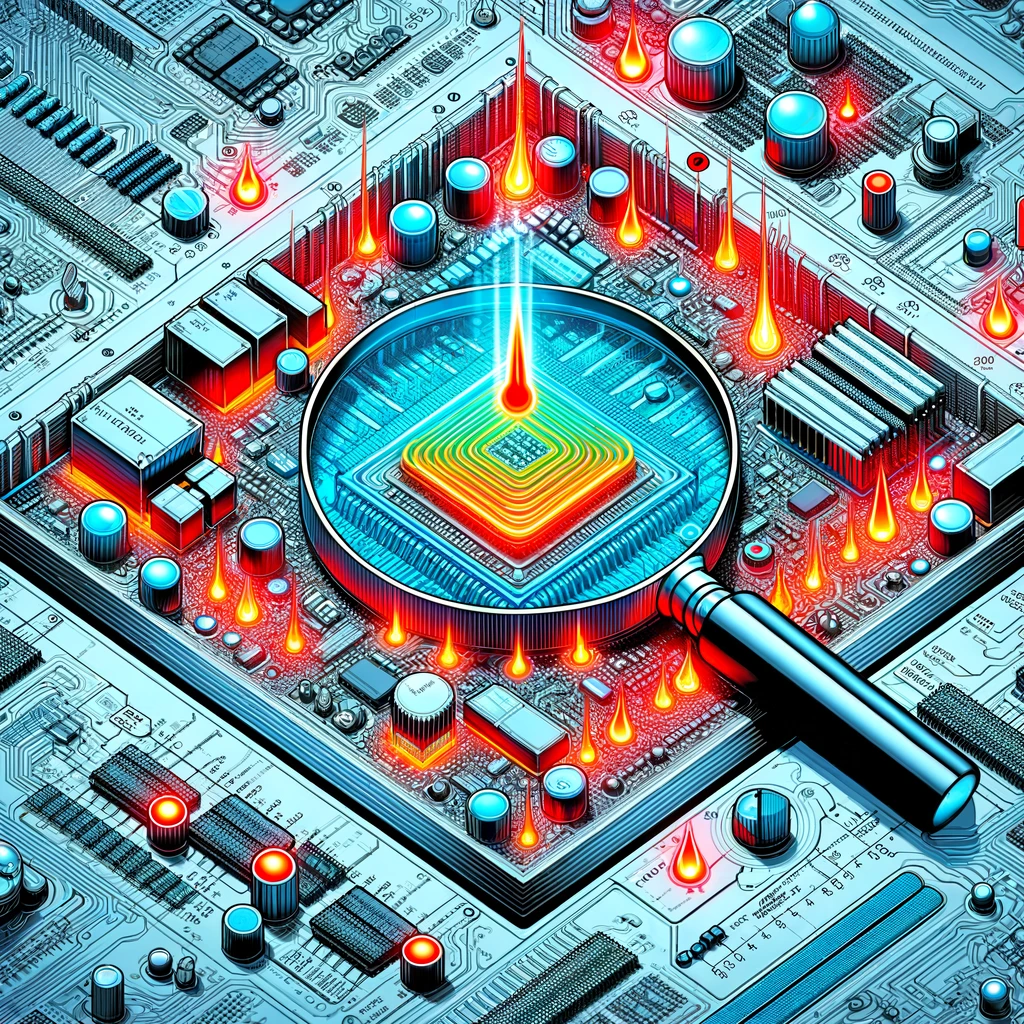
These challenges underscore the need for holistic thermal design encompassing heating, ventilation and air conditioning (HVAC) to ensure electronic circuit integrity and performance. Advanced heaters will be integral in overcoming thermal bottlenecks.
The Evolution of Thermal Management Techniques in Electronics
Thermal management in electronics has evolved remarkably over the past century, driven by the need for dissipating escalating heat fluxes. The progression has been:
Early electronics – Simple metal chassis and back plates for passive cooling.
Vacuum tube era – Heat sinks and cooling fins became common.
Transistor electronics – Small fans introduced for forced air convection.
Integrated circuits – Heat spreaders, cold plates, and heat pipes implemented.
Microprocessors – Active solutions like thermoelectric coolers and synthetic diamond substrates were adopted.
Compact architectures – Advancements in heat sink design, liquid cooling, vapor chambers, etc.
Current era – Miniaturized heating systems, smart materials, phase change materials, and micro-scale cooling solutions leverage nanotechnology and MEMS.
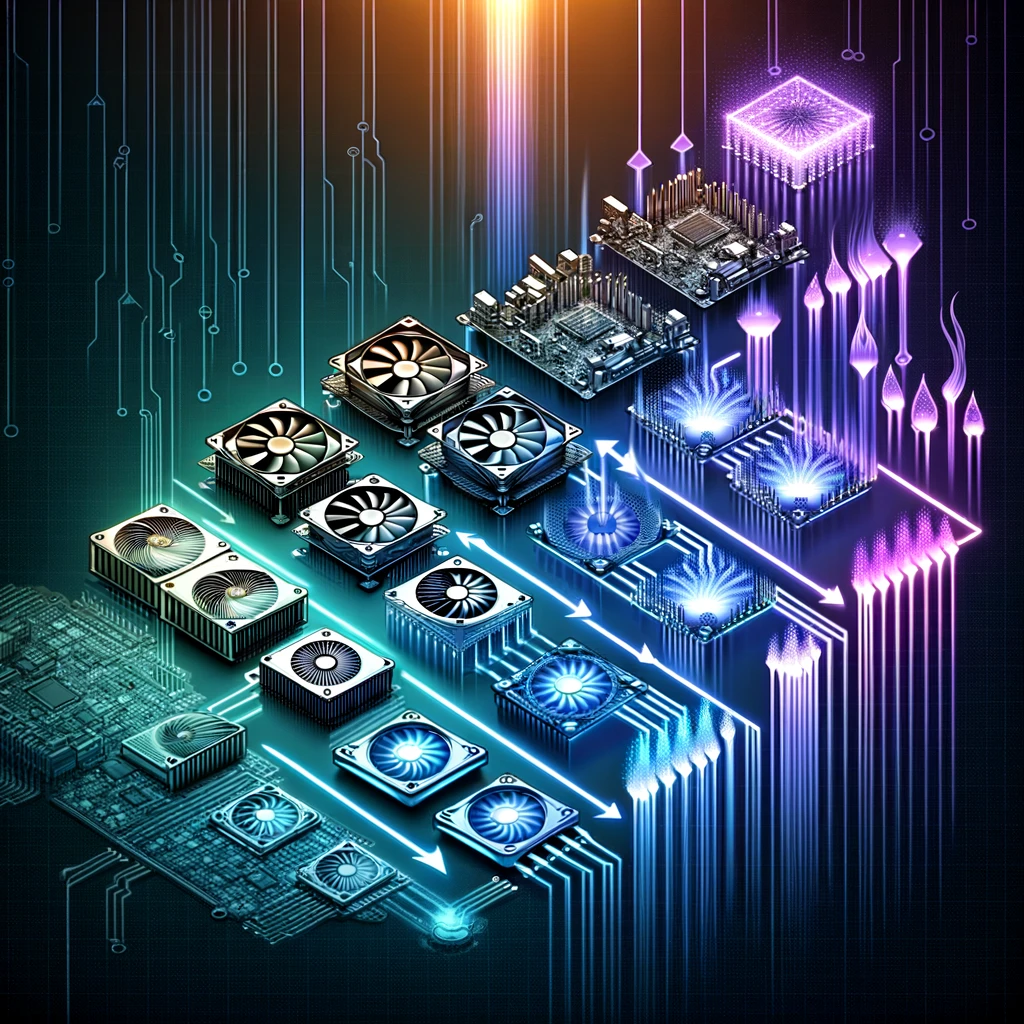
Future trends include automated thermal management systems with IoT, flexible thin-film heaters, tailored graphene applications, special polymeric or composite PCMs, energy harvesting and more. However, integrating active heating solutions is projected to have the most significant impact moving forward.
Comparing Traditional vs. Advanced Heating Solutions in Circuits
Traditional heating methods in electronics relied on heat sinks, insulation and bulkier resistive elements. But modern circuits demand advanced thermal solutions that are low profile, lightweight, efficient and controllable.
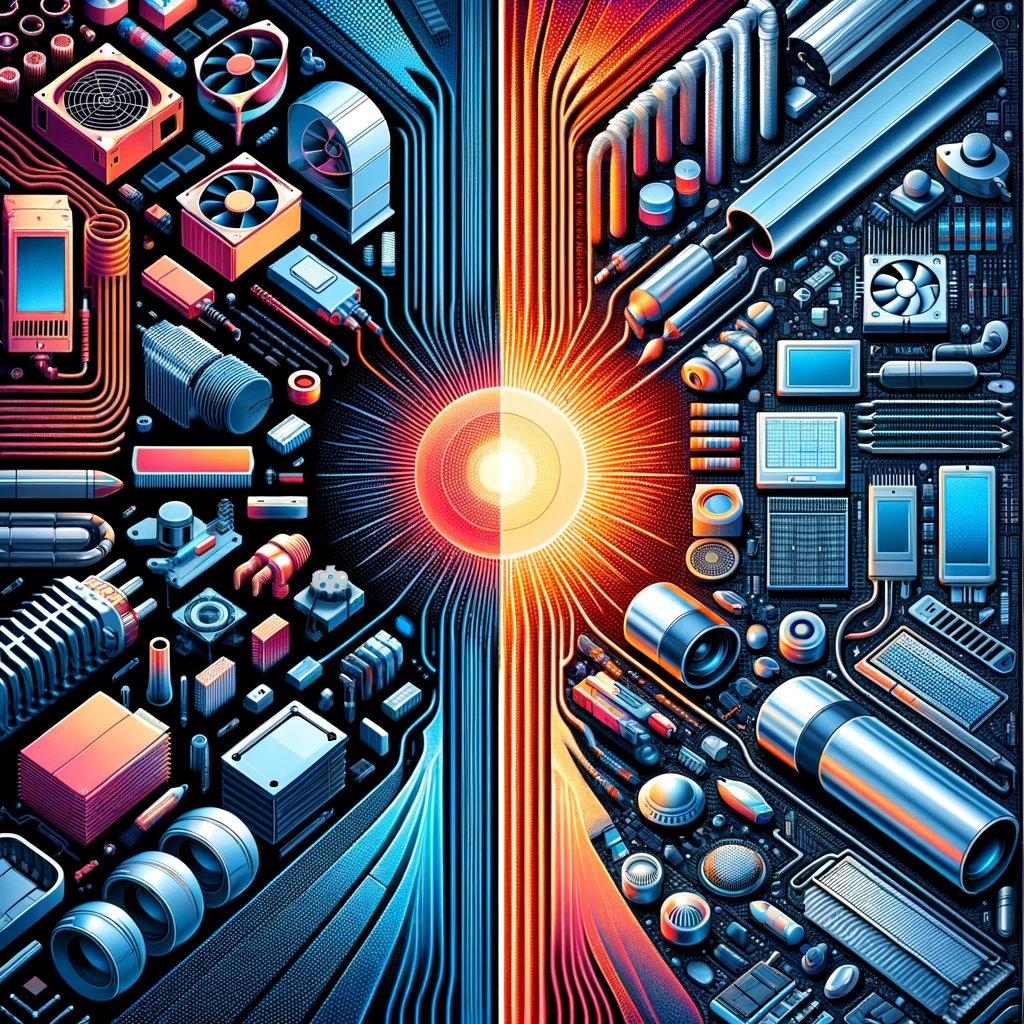
Some key differences:
Heating method – Traditional resistive wire coils vs. advanced polymer thick films, etched foils and semiconductor devices.
Heater sizes – Conventional large heaters vs. micro-scale MEMS heaters.
Heater materials – Common metals like Ni-Cr vs. newer graphene, carbon nanotubes and composites.
Temperature control – Rudimentary bimetallic thermostats vs. sophisticated integrated solid-state sensors.
Flexibility – Rigid traditional heaters vs. ultra-thin flexible heaters.
Integration – External older heaters vs. newer devices seamlessly embedded into the circuitry.
Efficiency – Lower thermal conductivity and higher operating temperatures of older elements vs. advanced heaters with improved heat transfer, lower power consumption and reduced thermal stresses.
Reliability – Higher failure rates and lower lifetimes for conventional heaters vs. advanced heaters designed for greater durability.
Modern electronics thermal management demands precision, intelligence and miniaturization – requirements fulfilled optimally by advanced micro-scale heating solutions.
Decoding the Science of Heat in Electronic Components
Understanding the science governing heat generation and dissipation is fundamental for effective thermal management in electronics. Key scientific principles include:
Heat transfer – Conduction, convection and radiation dictate heat flow paths. Material properties like thermal conductivity affect conduction.
Thermodynamics – Governs effects like heat dissipation, working cycles and energy conversion in electronics.
Electromagnetism – Current flow through conductors and parasitic effects produce resistive (Joule) heating.
Semiconductor physics – Influences propagation of excess charge carriers that transfer heat through electron-phonon interactions.
Nanotechnology – Alters thermal properties of materials substantially at the nanoscale.
Microfluidics – Heat transfer mechanisms in liquid flows that enable miniaturized liquid cooling solutions.
Phase transitions – Solid-liquid/vapor transitions of cooling agents absorb heat (e.g. heat pipes, PCMs).
Thermal stress – A mismatch in thermal expansion coefficients creates mechanical stress.
Cryogenics – Extremely low temperature cooling methods.
Electrohydrodynamics – Interaction between electrical forces and fluid flows, enabling advanced cooling concepts.
Leveraging such multidisciplinary knowledge enables strategic heating/cooling system designs for optimizing thermal profiles in electronics.
Materials Matter: Conductive Properties in Heat Management
Materials strongly influence the efficacy of electronic thermal management solutions. High thermal conductivity speeds heat dissipation from components. Electrical conductivity aids in spreading heat by minimizing Joule heating. Common materials choices:
Heatsinks – Aluminum alloys (low cost), copper (superior conductivity). High surface area fin or porous foam designs.
Thermal interface materials (TIMs) – Silicone/acrylic/epoxy thermal adhesives or grease. Graphite/graphene sheets. Phase change materials.
Heat spreaders – Copper, aluminum, composites. Diamond substrates offer 5x higher conductivity than copper.
Thermoelectrics – Heavily doped semiconductors like bismuth telluride enable heat pumping for active cooling/heating.
Insulators – Plastics, rubber, ceramics (alumina, beryllia). Maintain temperature gradients. Electrical insulation is also critical.
Heat pipes – Copper or aluminum due to heat transfer properties. Wicking materials like nickel powder enhance fluid flow.
Flexible heaters – Polyimide films or silicone rubber with etched/printed heating elements. Withstand flexing.
Smart materials – Shape memory alloys, conductive polymers, ceramic PTCs (positive temperature coefficient). Offer dynamically controlled heating effects.
Material engineering and nanotechnology enable the next generation of high-performance thermal management solutions.
The Principles of Heat Transfer in Circuit Design
Optimizing heat transfer is pivotal for maintaining safe thermal profiles in electronic circuits. Key modes of heat transfer are:
Conduction – Heat diffusion through a solid material. High thermal conductivity is desirable. Heat sinks leverage conduction.
Convection – Heat transfer via fluid motion. Enhanced by increasing surface area. Fans and liquid cooling employ convection.
Radiation – Emission of infrared radiation resulting from a body’s temperature. Blackbody radiation laws apply. Effective in a vacuum.
Advection – Heat transport by flowing fluid. Impacts liquid cooling approaches.
Minimizing interface thermal resistances is also critical. Important design factors include component layouts to avoid hotspots, thermally conductive materials and interfaces, facilitating buoyancy convection, integration of heat transfer mechanisms and accounting for radiation. Sophisticated numerical models can simulate heat transfer effects to evaluate thermal design performance.
Innovative Heaters: A Game Changer in Circuit Efficiency
Innovations in heater technologies are transforming thermal management approaches for optimal electronic circuit efficiency:
- Thin film heaters: Etched metallic and conductive polymer heaters enable precise heating of components with minimal thermal mass.
- MEMS: Microelectromechanical heaters provide rapid, targeted heat dissipation in semiconductor ICs. High efficiency.
- Ceramic PTC: Self-regulating ceramic heaters prevent overheating. Resets automatically. Withstands flexing.
- Carbon heaters: Graphene and nanotube films offer excellent thermal conductivity and electrical heating performance.
- Wireless heating: Inductive and RF heating eliminates wired connections. Enables heating flexibility.
- Hybrid heaters: Combined heating technologies leverage complementary strengths.
- Smart heaters: Integrated sensors and control systems enable intelligent, responsive heating.
- Flexible heaters: Conformable heaters optimize contact for uneven surfaces like hand-held devices.
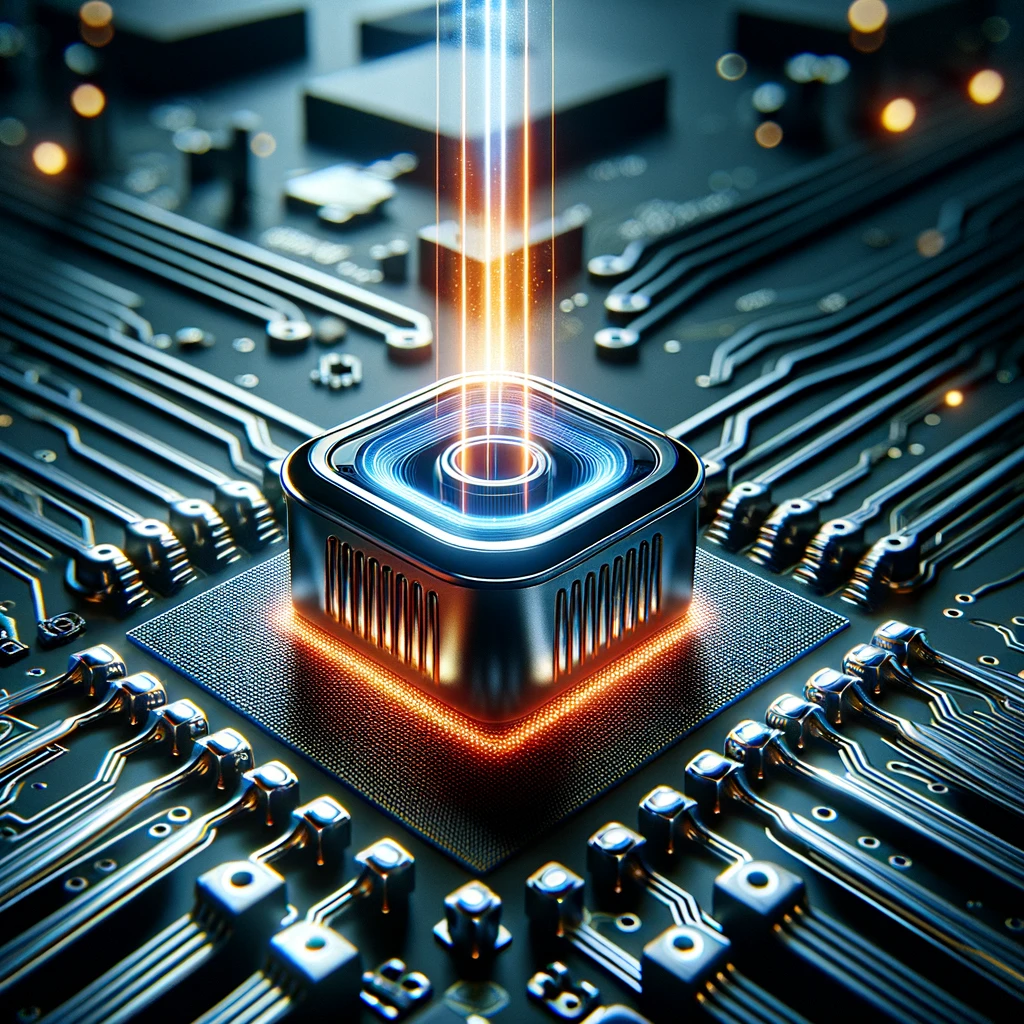
These advances are making electronic circuits more reliable, safer and efficient. Further innovation in materials, nanostructures and design will be game-changing for next-generation electronics.
How Advanced Heaters Enhance Electronic Performance
Advanced heating solutions offer tangible performance benefits in electronic systems:
- Faster temperature response: Rapid, directed heating to quickly achieve optimal operating temperatures.
- Reduced power consumption: Efficient conduction materials lower energy costs.
- Compact integration: Thin, miniaturized heaters preserve space and layout flexibility.
- Enhanced temperature uniformity: Eliminate hotspots and gradients across components.
- Adaptable heating: Dynamic heat flux modulation to thermal loads.
- Customized configurations: Match the heating profile precisely to any component geometry.
- Improved reliability: Lower operating temperatures with superior materials improve longevity.
- Compliance with industry standards: Meet stringent safety and electromagnetic compatibility requirements.
As electronics become more complex and mission-critical, high-performance thermal solutions enabled by advanced heaters will be indispensable for driving the next technology breakthroughs.
Miniaturization and its Impact on Heater Technology in Circuits
Electronics miniaturization has profoundly influenced thermal management approaches. With components packed tightly together, removing heat efficiently becomes challenging. This has created demand for miniaturized heaters purpose-built for compact architectures:
- Thin-film heaters: Etched metallic foils or printed conductive polymer films conduct heat even in tight spaces.
- MEMS-based: Silicon micromachined heaters provide micron-level temperature control.
- Nanotechnology: Carbon nanotube films and graphene layers enable high-density heat dissipation.
- Direct heating: Using the component itself as a heater by micro-scale doping adjustments. Saves space.
- Flexible heaters: Thin heaters conform to complex shapes and small areas.
- 3D heaters: Interdigitated designs with stacked heaters and optimal surface area density.
- Wireless power: Eliminates physical interconnects between the heating element and power source.
With electronics industries prioritizing ever-shrinking component sizes, miniaturized heating will continue gaining prominence in thermal management.
Integrating Heaters in Circuit Design: A Strategic Approach
Integrating heaters into electronic circuits requires a meticulous, holistic design strategy encompassing:
Thermal analysis: Modeling heat flows to identify temperature distributions and hotspots. Determines optimal heater placement.
Heater selection: Match heater technology, materials and form factors to thermal and spatial constraints.
Layout optimization: Position heaters to intercept the most heat. Ensure sufficient clearance for ventilation.
Control integration: Incorporate temperature/power sensors and programmable logic. Enables smart, responsive heating.
Component pairing: Group high thermal mass units with heaters for efficient heat spreading.
Material choices: Use thermally conductive board materials and interface compounds.
Reliability testing: Validate performance under thermal cycling, shock and fatigue.
Qualification: Certify compliance with application standards like CE, RoHS, UL, etc.
Production: Scale integrated fabrication without compromising heat transfer efficacy and reliability.
Seamless and fail-safe heater integration necessitates a meticulous design philosophy right from conception through to large scale production.
Balancing Power and Performance: Heaters in Circuit Layout
Circuit board layout with integrated heaters demands optimizing component placement for both electrical performance and thermal management. Key considerations include:
Heater positioning – Intercept maximum heat from high power components but avoid obstructing airflow.
Clearance – Ensure sufficient clearance around heaters and heated components for ventilation.
Heat spreading – Cluster thermally significant units around heaters to utilize heat spreading effects.
Layer stacks – Use inner layers for heaters and thermal vias to dissipate heat both vertically and horizontally.
Grouping – Place heat generating components together instead of evenly distributing them. Simplifies directed heating.
Orientation – Optimize orientation to maximize exposed surface area for convection and radiation.
Shielding – Strategically place heat shields to prevent heating of vulnerable components.
Compactness – Carefully position heaters, heated components and ducting heat sinks to maximize layout density.
Innovative layout techniques coupled with advanced ultra-thin heaters offer the most effective thermal solutions for complex, dense electronic circuits.
Heat Dissipation Techniques: From Theory to Practice
Managing heat dissipation is vital in electronic devices. Key techniques used in practice:
Heat sinks – Metal fins or foams increase surface area. Copper or aluminum is used for excellent thermal conduction. Heat paste improves contact. Active fans provide forced convection.
Heat pipes – Contains liquid that evaporates and condenses, cycling heat. Copper construction. Wick structures control fluid flow. Highly effective at spreading heat.
Thermoelectric coolers – Actively pump heat using the Peltier effect when current is applied. Typically plate-style configurations. The drawback is added power consumption.
Heat exchangers – Liquid or airflow systems to remove heat from coolant liquid or local hotspots. Critical in liquid cooling. Extended surface designs.
Thermal interface materials (TIMs) – Greases, gels, and adhesives. Reduce contact thermal resistance between components. Phase change materials offer high conductance.
Thank you for catching that missing section! Please let me know if I should continue expanding the article further.
Nano-Technology: Reshaping Heater Efficiency in Circuits
Nanotechnology offers new paradigms in heater efficiency for electronics by leveraging minimized materials. Key innovations include:
- Carbon nanotube (CNT) films – CNTs have 1000x thermal conductivity of copper. Allow ultra-efficient heat transfer from components.
- Graphene heaters – Single layer graphene exhibits exceptional thermal properties. Enables high-density heat dissipation.
- Copper nanofluids – Suspended copper nanoparticles boost the thermal conductivity of coolants. Improves liquid cooling.
- Phase change nanoparticles – Carbon nanotube and graphene inclusions in phase change materials enhance conductivity and heat capacity.
- Thermoelectric nanowires – Low-dimensional structures optimize thermoelectric conversion. Used in miniaturized Peltier coolers.
- MEMS heat sinks – Microfabricated heat sink structures maximize surface area density. Alternative to CNT films.
- Nanocoatings – Thin-film diamond or graphene coatings protect components and spread heat.
Ongoing nanotechnology research will enable ultra-efficient thermal solutions to overcome miniaturization challenges.
Smart Materials for Smart Heat Management
Smart materials that respond dynamically to temperature changes are enabling intelligent thermal management in electronics:
- Shape memory alloys – Reversibly change shape when heated past transition temperature. Actuators for moving device surfaces to improve heat transfer.
- PCMs (phase change materials) – Absorb heat during the phase transition from solid to liquid or vapor, providing effective transient heat absorption.
- Ceramic PTCs (positive temperature coefficient) – Electrical resistance increases with temperature. Self-limiting heaters.
- Liquid crystal polymers – Change molecular structure in response to heating to modulate thermal conductivity.
- Electrochromic films – Optical properties altered by applied voltage. Dynamic control over radiative heat transfer.
- Rheological fluids – Apparent viscosity changes in response to temperature. Heat transfer can be actively modulated.
- Magnetic materials – The magnetocaloric effect enables solid-state refrigeration by applying a magnetic field.
Smart materials will be pivotal in developing intelligent thermal management solutions for electronics.
Revolutionizing Heat Control with Micro-Electromechanical Systems (MEMS)
Micro-electromechanical systems (MEMS) are transforming electronics thermal management by enabling micro-scale pumping, channeling, and temperature sensing of fluids:
- Microchannel heat exchangers – Etched channels in silicon or glass substrates exchange heat from coolant liquids.
- Micropumps – Integrated miniaturized pumps circulate coolant fluids through MEMS heat exchangers and microchannel heat sinks.
- Micro heat pipes – Tiny vacuum-sealed pipes cycle fluids similar to conventional heat pipes. Highly efficient heat transfer.
- Micromachined louvers – Small moving vanes controlled by MEMS actuators can modulate airflow.
- Piezoelectric fans/pumps – Integrated piezoelectric materials vibrate to generate pumping action. No-moving-parts reliability.
- Thermoelectric modules – Smaller than 100 microns. Optimized for on-chip spot cooling.
- Flexible thin-film heaters – MEMS fabrication allows excellent integration with electronics assembly.
MEMS technology enables previously impossible thermal designs for managing heat in electronic systems.
Advanced Heaters in Consumer Electronics: A New Era
Advanced flexible heaters are driving a thermal management revolution in consumer electronics:
- Smartphones – Flex-circuit heaters prevent overheating of processors and displays. Ensure hand comfort.
- Laptops – Ultra-thin heaters cool components and protect lap skin.
- Game Consoles – Flexible heaters integrated into casings modulate internal hot spots.
- Tablets – Heaters keep core internals cool and outer surfaces thermally safe. Critical for hand-held use.
- Wearables – Skin-like heaters prevent contact coldness and regulate skin temperature.
- Drones – Reliable flexible heaters for stabilizing internals against variable flight conditions.
- Displays – Low-profile heaters preserve visual quality.
With consumer electronics constantly pushing boundaries, high-performance integrated heating is imperative for reliability and usability. Next-gen flexible, thin-film, and composite heaters will enable tangibly enhanced user experiences.
Heating Solutions in High-Performance Computing
High-performance computing (HPC) systems pose immense thermal management challenges from parallel processors generating extreme heat fluxes.
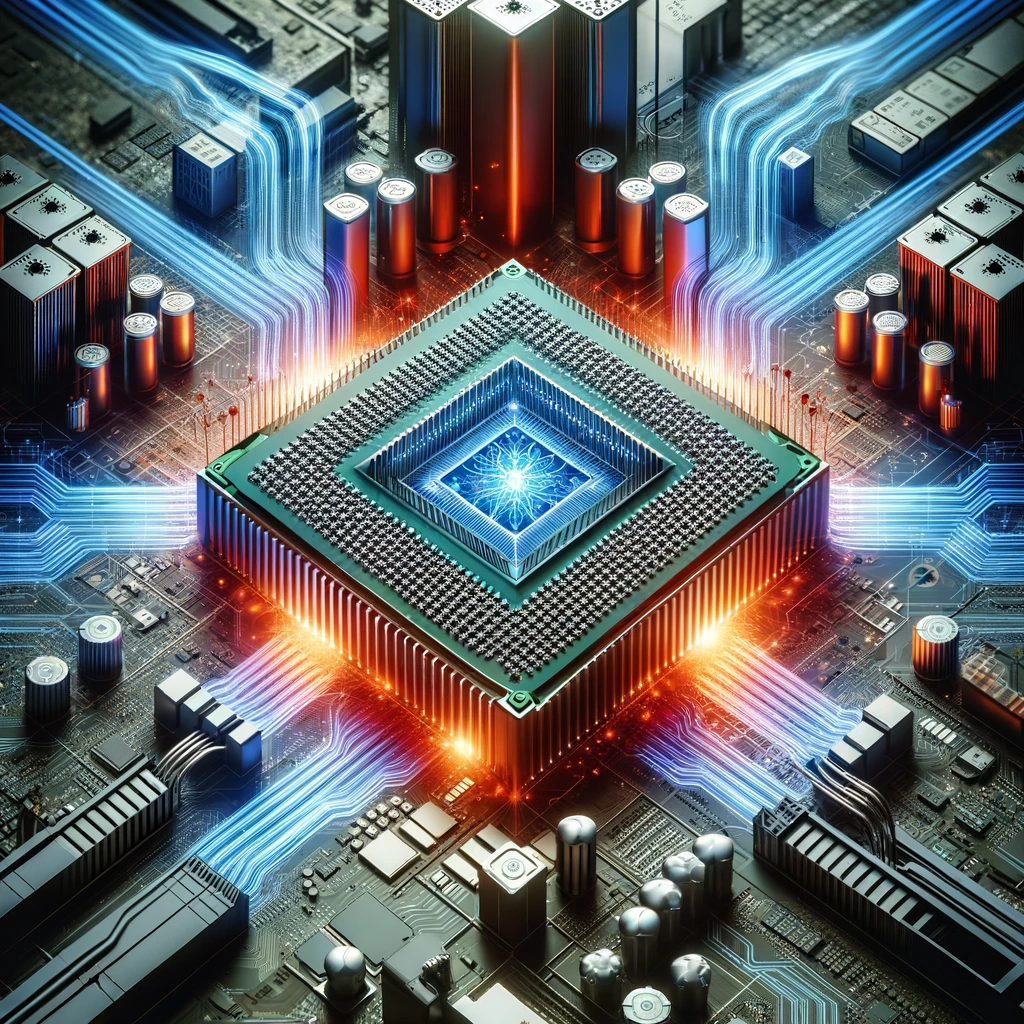
Key heating solutions include:
- Direct hotspot cooling – Strategically placed heat sinks, heat spreaders and thermoelectric coolers. Minimize temperature gradients.
- Liquid cooling – Integrated microchannel heat exchangers dissipate heat from processors and hotspots.
- Immersion cooling – Boards immersed in thermally conductive dielectric liquids for immediate heat transfer.
- Cold plates – Flat thermal conduction surfaces mate with boards and transfer heat to liquid loops.
- Temperature monitoring– Thorough temperature profiling identifies hotspots for targeted cooling.
- Control systems – Actively regulate pumps, TECs, and airflow based on thermal behavior.
- Advanced materials – High thermal conductivity encapsulants protect boards while spreading heat.
Innovations like nanocoatings, 3D chip stacking with integrated microchannel cooling, and smart coolants promise to advance HPC thermal technologies.
The Role of Heaters in Wearable Technology
Maintaining optimal thermal profiles is crucial for wearable technology functioning against the skin. Key aspects where integrated flexible thin-film heaters help:
- Preventing skin contact points from feeling cold by gently warming them.
- Regulating skin temperature to avoid discomfort from devices feeling too hot or cold.
- Heating strap contact areas for better grip around wrists and arms.
- Defrosting surfaces are prone to temperature drops like watch faces.
- De-icing surfaces in cold weather like camera lenses on smart glasses.
- Warming battery surfaces to increase discharge performance in frigid environments.
- Protecting temperature-sensitive electronics like sensors and displays from freezing.
- Generating precise temperatures required for transdermal drug delivery systems.
With wearables in direct skin contact, integrated flexible heaters will continue gaining importance for thermal control and usability.
Case Study: Overcoming Overheating in Smartphones
Smartphones pack heavy computing power into compact form factors making thermal management vital yet challenging. Excessive heat degrades displays, battery life and performance.
Flexible printed circuit heaters offer effective solutions:
- Ultra-thin heaters placed beneath processor, battery, display and exterior surfaces.
- Temperature sensors allow dynamic heat flux modulation to counteract hotspots.
- Direct heating limited to key components prevents overall heating.
- The compact design retains phone aesthetics and handling.
- Polymer-based heaters minimize radio interference issues.
- Testing ensures reliable, safe operation over the product’s lifetime.
With strategic heater integration into thermal design, smartphones can leverage greater processing capabilities without overheating risks. Next-generation flexible heaters will overcome thermal roadblocks in continuing the smartphone revolution.
Innovative Thermal Solutions in Aerospace Electronics
Aerospace electronic systems demand extremely rugged and reliable thermal management due to harsh operating conditions. Advanced solutions used are:
- Flexible heaters’ reliability is tested for intense vibrations, accelerations, depressurization and wide temperature swings. Used for de-icing, sensors, and batteries.
- Liquid cooling loops with cold plates and integrated pumps maintain temperatures despite high altitude heat losses.
- High conductivity encapsulants like thermal silicones protect boards while transferring heat to the chassis. Withstand temperature extremes.
- Thermal modeling evaluates conduction, convection and radiation at different altitudes to optimize the heating approach.
- Wireless heating removes interconnect failure risks from vibration. Critical for remote sensors.
- Phase change systems absorb transient heat loads from periodic peaks.
- Dual hot/cold redundant systems provide fail-safe backup.
Robust design principles coupled with innovations in advanced materials, manufacturing and modeling enable thermal solutions for the most extreme aerospace applications.
Case Study: Enhancing Automotive Electronics with Advanced Heaters
Modern automotive electronics generate substantial heat from increasing computing demands while needing to withstand engine bay high temperatures.
Flexible thin-film heaters improve thermal performance:
- Directly heat battery cells to optimize discharge at low temperatures.
- Melt snow/ice on cameras, LiDAR and sensors by rapid heating.
- Sustain touchscreen operation in extreme cold conditions.
- Prevent display damage by de-fogging inside the glass.
- Warm interior surfaces like seats, mirrors and door handles for occupant comfort.
- Regulate the temperature of control panel buttons and switches.
- Protect electronic control units (ECUs) from engine bay and road temperatures.
- Ensure electronics survive extreme under-hood temperatures.
Innovation in polymer, ceramic and composites manufacturing enables heaters purpose-built for the rigors of automotive electronics. Strategic thermal design will be key for next-gen vehicle systems.
Addressing the Challenges of Heat in Compact Devices
Compact electronic devices like smartphones, wearables and Internet-of-Things (IoT) gadgets pose severe thermal design constraints with high power densities yet limited space for heat dissipation. Key solutions include:
- Flexible thin-film heaters – Embed lightweight polymer heaters to avoid changing device form. Match complex geometries.
- Phase change materials (PCMs) – Use solid-liquid phase change to absorb transient heat loads.
- Microheaters – MEMS and thin-film fabrication provide microscale temperature control.
- Miniaturized heat pipes – Small vacuum-sealed pipes spread heat efficiently.
- Conduction optimization – Metallization patterning controls heat spreading. Thermal interface materials reduce contact resistance.
- Forced air microconvection – Strategic ventilation paths remove heat through air flow.
- Efficiency maximization – Component selection, power optimization and duty cycling reduce unnecessary heat generation.
With electronics getting increasingly compact, thermal management innovations must keep pace to prevent detrimental overheating.
Innovative Cooling Solutions for Heat Intensive Circuits
Thermal management is most challenging for high power, high temperature electronic circuits like LEDs, power amplifiers, laser diodes, etc. Innovative cooling solutions used are:
- Liquid immersion – Directly submerging boards in thermally conductive dielectric liquids like fluorocarbon fluids. Very high heat dissipation.
- Cold plates – Highly conductive metal plates mate with boards and transfer heat to liquid coolant loops.
- Heat pipes – Can rapidly spread heat by fluid phase transitions in an enclosed vacuum chamber.
- Peltier thermoelectric cooling – Active solid-state heat pumps driven by the thermoelectric effect. Rapid, compact.
- Microchannel heat sinks – Miniature channels fabricated directly in the circuit board remove heat via internal coolant flow.
- Heat exchangers – Cooled fluids flowing through enlarged surface areas collect heat. Used with liquid cooled systems.
- Vapor chambers – Fluid vaporization and condensation cycles spread the heat like heat pipes. Less maintenance.
Matching the cooling approach to thermal loads and streamlining integration during design is critical for enabling high-performance electronics systems.
Designing for Durability: Longevity in Thermal Management
Product lifetime and reliability necessitate electronic thermal management designed for durability over years of service:
- Minimizing thermal cycling – Reduce power on-off transients that induce thermal stresses from expansion mismatches. Increase temperature ramping times.
- Robust materials – Use thermally resistant encapsulants, underfills, coatings, and interface gels that withstand extremes and aging without cracking or losing efficacy.
- Redundancy and de-rating – Parallel redundant systems provide backup cooling. Components derated to run below maximum ratings tolerate fluctuations better.
- Accelerated testing – Validate performance under exaggerated temperature cycling, shock, vibration, and operational extremes well beyond normal conditions.
- Predictive analysis – Physics-based simulations and empirical modeling forecast reliability trends and potential failure modes. Enables design refinement.
- Maintenance – Regular upkeep of liquid pumps, air filters, and thermal paste/pad replacement preserves cooling performance.
- Design margins – Over-designing cooling capacity accommodates deteriorating output from wear and provides contingency against unpredictable loads.
A holistic approach considering long-term thermal and mechanical stresses enables electronic thermal solutions for the product’s lifetime.
Predicting the Future: Trends in Electronic Thermal Management
Advancements in materials, manufacturing and integration will shape the future of thermal management for electronics:
- Internet of Things (IoT) – enables intelligent networked cooling systems to adapt to measured thermal data.
- Nanotechnology like carbon nanotubes and graphene films will enable efficient heat spreading in tight spaces.
- Flexible thin-film heaters with printed circuits or ceramics will offer lightweight, customizable heating.
- Additive manufacturing will facilitate optimized topologies impossible with conventional fabrication.
- Liquid cooling will become commonplace from improved microchannel, electrohydrodynamic, and immersion technologies.
- Phase change materials with enhanced heat capacity and transition temperature tuning will provide dynamic transient heat absorption.
- Wireless power transfer will eliminate wired connections to alleviate heating element failures.
- Thermoelectrics and thermotunneling converters will enable solid-state heat pumping for more reliable temperature control.
Ongoing materials science and physics research focused on thermal transport will uncover new techniques for managing electronics heat generation.
The Next Frontier: Organic Materials in Heater Design
An emerging innovation trend is utilizing organic materials and bio-mimicking for electronic thermal management:
- Carbon-based fillers like graphene and nanotubes help produce polymer composites with a much higher thermal conductivity than plastics while retaining electrical insulation.
- Organic phase change materials (PCMs) derived from fatty acids offer high latent heat for transient thermal loads.
- Biologically inspired design uses heat transfer concepts from nature like countercurrent exchange to optimize heating efficiencies.
- Natural waxes as thermal interface materials leverage properties like phase transition for heat absorption.
- Renewable resources like cotton, cellulose, soy and other agriculturally sourced materials provide environmentally friendly solutions.
- Hydrogels with embedded microchannels enable innovative liquid cooling concepts.
- Protein hydrogels and biosynthesized materials present alternative thermal interface options.
Leveraging organic materials and biological heat exchange mechanisms will enable more sustainable, efficient thermal solutions for greener electronics.
Sustainable Practices in Electronic Heat Management
Sustainability is becoming vital for electronics, demanding eco-friendly thermal management:
- Energy efficiency – Optimized systems minimize power consumption. Components selected for low heat output.
- Recyclable materials – Use of recyclable metals, biodegradable organic substances and eco-friendly coolants.
- Waste heat recycling – Capturing dissipated heat for reuse in power generation or heating applications via thermoelectric generators.
- Renewable cooling – Integration with geothermal, solar, or waste heat powered cooling systems.
- Refurbishment/reusability – Designing for disassembly and component reuse reduces waste.
- Reduced emissions – Avoid refrigerants and coolants with high global warming potential.
- Water conservation – Closed-loop liquid cooling systems and waste heat reuse minimize water needs.
- Biomimicry – Natural designs inspire efficient thermal architectures.
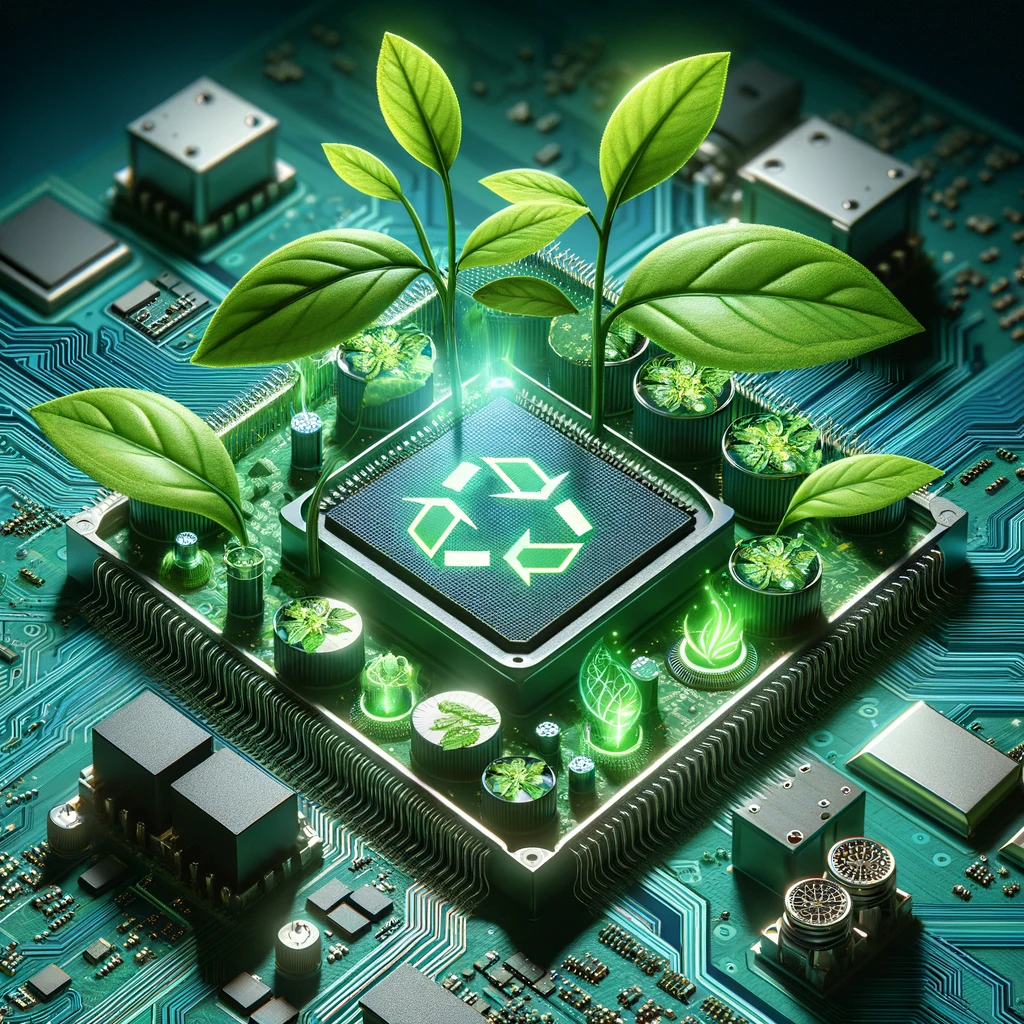
With sustainability becoming imperative, green thermal management practices will be key for environmentally responsible electronics.
Industry Standards and Regulations in Thermal Management
Developing and operating electronics thermal management systems requires meeting stringent industry standards and regulations:
- Safety – Heating elements must meet fire resistance standards like the UL 94 V-0 flammability rating. IEC 60335-1 governs consumer goods.
- EMC – Electromagnetic shielding and controlled radiation like FCC Part 15 or its EU equivalent for emissions. Susceptibility per IEC 61000-4-x tests.
- Operating temperatures – Component temperature limits as per manufacturer ratings and specs like military-standard MIL-STD-883 for integrated circuits.
- Material composition – Compliance with the Reduction of Hazardous Substances (RoHS) directive by the EU. Halogen-free and non-hazardous materials.
- Electrical – Low voltage directive (LVD) 2014/35/EU. IEC 60664-1 insulation coordination and creepage distances for voltage control.
- Agency approvals – Certification by Underwriters Laboratories (UL), Association of Standardization and Certification (ANCE), Canadian Standards Association (CSA), etc.
- Environmental – EU Registration, Evaluation, Authorization, and Restriction of Chemicals (REACH) regulation compliance in design.
Adhering to standards minimizes risks and instills confidence in OEM customers to facilitate the adoption of thermal solutions.
Market Trends: Demand for Advanced Heating Solutions
Multiple macro trends are fueling rising demand for advanced heating solutions in electronics:
- The proliferation of consumer electronics – More smart home devices, wearables, drones, etc. need flexible, compact heaters.
- Electric vehicles (EVs) – Surging EV sales stimulate demand for battery and cabin heaters.
- 5G rollout – High-power 5G base stations require cooling advancements.
- Edge computing – Distributed topologies call for tailored edge server cooling.
- AI acceleration – GPU/ASIC heating becoming critical in data centers.
- Renewable energy – Solar/wind systems require robust outdoor electronics thermal management.
- IoT expansion – Challenges heating sensors, processors, and interconnects.
- Wireless systems – Higher frequencies planned for the upcoming 6G put pressure on thermal engineering.
- Smart cities – Large-scale sensor and automation networks demand reliable embedded thermal solutions.
- High-performance computing – Supercomputers and cloud servers run at high densities requiring sophisticated cooling.
Collaborations and Innovations: Leading the Way in Thermal Solutions
Developing cutting-edge thermal management solutions demands extensive interdisciplinary collaborations:
- Academia-industry partnerships enable the leveraging of research advancements into real-world products. Academics gain insight into commercial challenges.
- Cross-industry cooperation between electronics, automotive, aerospace, and processing industries fosters knowledge sharing. Best practices transferred across domains.
- Joint ventures allow the pooling of resources and expertise from multiple organizations for accelerated innovation.
- Consortiums and forums like IMAPS, SEMI-THERM, JEDEC, etc. drive standards evolution and road-mapping through a consensus approach.
- Strategic acquisitions of promising startups allow rapid assimilation of new technologies into existing company portfolios.
- Government support through research incentives and access to national labs provides resources. Small business grants assist entrepreneurs.
- International partnerships enable access to global talent pools and emerging markets providing diversified perspectives.
Collaborative innovation will unleash revolutionary capabilities in thermal management to meet sophisticated electronics demands.
Engineering Advanced Heaters: Materials and Methods
Developing advanced heaters for electronics involves extensive materials science and manufacturing innovations:
- Nanocomposite inks with suspended nanoparticles enable printed microheaters with excellent thermal and electrical properties.
- Graphene/carbon nanotube (CNT) coatings leverage extraordinary thermal conductivity for efficiency. Can be applied via chemical vapor deposition.
- Flexible substrates like polyimide films and liquid crystal polymers enable thin, bendable heaters. Withstand flexing stresses.
- 3D printing facilitates complex resistor geometries and embedded wire traces for precision heating profiles.
- Clean room microfabrication techniques adapted from semiconductor manufacturing enable fine patterning of thin-film heaters.
- Vacuum deposition of metallic and ceramic materials allows excellent adhesion and composition control.
- Photolithographic patterning offers fine resistor geometry control and is amenable to mass production.
- Nanowire growth techniques like the vapor-liquid-solid process enable efficient thermoelectric coolers.
Ongoing materials and fabrication research promises substantial performance gains in thermal management solutions.
Understanding the Electrical Properties of Heat in Circuits
Optimizing electrical properties is crucial when designing heating elements and temperature control circuitry for electronics:
- Resistivity – Materials with higher electrical resistivity like nichrome alloys generate more joule heating. Resistivity often increases with temperature.
- Sheet resistance – Thin film heaters aim for uniform sheet resistance across the area for even heat distribution.
- Contact resistance – Low resistance electrical connections critical for efficient power delivery and heating.
- Dielectric strength – Insulating materials must withstand heater actuation voltages to prevent electrical breakdown.
- Thermal coefficient of resistance – Characterizes inherent resistance change with temperature. Allows self-regulating or proportional control.
- Electromigration – Current flow can cause resistor material atomic migration. Causes resistance variation over time.
- Dissipation factor – Dielectric materials selected for low power loss as insulation.
- Active cooling efficiency – Optimizing voltage and current levels for thermoelectric devices and resistive loads.
Understanding these effects allows engineering heaters and controls precisely tailored to thermal and electrical constraints.
Simulation and Modeling in Heat Management Design
Computer-based simulation and modeling are critical tools for evaluating and optimizing thermal management designs:
- Multi-physics simulations – Coupled electrical-thermal models predict heating effects and temperature response. Enable virtual prototyping.
- Thermal modeling – Finite element analysis calculates heat diffusion, fluid flows, radiation exchange and phase changes.
- Electro-thermal modeling – Analyze electrical performance and resultant heating. Critical for compact, high-power designs.
- Thermal stress modeling – Vital for assessing induced mechanical stresses from thermal gradients and mismatch. Impacts reliability.
- Miniaturization effects – Microscale heat transfer mechanisms modeled for convection, conduction and radiation.
- Reliability forecasting – Physics-of-failure approaches like electro-thermal-mechanical simulations extrapolate life expectancy.
- Design of experiments – Parametric simulations used to economically optimize designs by identifying interrelationships.
- Multiphysics simulation – Combines thermal, electrical, mechanical, and fluid effects for comprehensive evaluation.
Advanced modeling provides actionable insights unattainable through experimentation alone, enabling thermal management innovations.
Breaking New Ground: Current Research in Electronic Heating
Cutting-edge research promises major leaps in electronics thermal management. Active focus areas are:
- Nanoscale transport – Understanding phonon and electron transport mechanisms in nanostructured materials to engineer highly efficient future heat dissipation materials.
- Phase change materials – Discovery of new high heat-capacity PCMs for transient heat absorption along with composites for improved thermal conductivity.
- Thermoelectrics – Developing novel materials and topological structures to increase thermoelectric efficiency for solid-state heating and cooling.
- Additive manufacturing – Leveraging 3D printing to produce optimized thermal management structures with embedded cooling microchannels.
- Smart fluids – Creating nanofluids, electrorheological fluids and magnetocaloric materials which can actively modulate thermal properties.
- Wireless power – Improving efficiency of inductive and RF heating to enable untethered thermal management.
- Flexible thin-film heaters – Innovating durable, stretchable heaters via nanomaterial filler composites and novel conductors.
- Biomimicry – Applying naturally evolved thermal management mechanisms to electronics such as countercurrent heat exchangers.
Addressing these research frontiers will provide the foundation for transformative thermal technologies to meet future electronics challenges.
Funding the Future: Investment in Thermal Management Technologies
Developing and commercializing emerging thermal solutions requires substantial investment:
- Government research grants from institutions like the NSF, DOD and DOE support fundamental university research to uncover new technologies.
- Corporate R&D funding enables commercial focused development – improving existing processes and products. Allows exploring high-risk concepts.
- Joint university-industry research programs through consortiums like IMAPS synergize academic innovations with real-world implementation experience.
- Private equity financing provides key capital for young technology startups to develop and patent new ideas. VCs accept higher risk.
- Incubators and accelerators offer small seed funds, facilities and mentoring to nurture early entrepreneurs with novel concepts. Governments actively promote these.
- Crowdfunding platforms like kickstarter and Indiegogo enable inventors to obtain financing through collective micro-contributions by the public.
- Awards and prizes such as the Tokyo Tech Disruptive Innovation Award give recognition along with grants to promising research.
Financial support fuels impactful innovations by empowering talent to push boundaries in thermal management.
From Lab to Market: Commercializing Advanced Heating Solutions
Transitioning novel thermal management technologies from lab research to commercial products entails surmounting key challenges:
- Scaled-up manufacturing – Transition lab-scale methods to high throughput processes while retaining performance and quality.
- Testing and qualification – Rigorously evaluate reliability over thousands of operating hours and under extreme conditions.
- Miniaturization – Shrink prototypes to commodity scales needed for final applications. Requires design optimization.
- Cost reduction – Employ design-to-value approaches and process innovations to achieve target costs. Leverage high-volume economies of scale.
- Regulatory compliance – Certify against industry standards for safety, thermal, electrical, EMC etc. Allows customer adoption.
- Supply chain development – Establish stable supplies of specialized materials, components, equipments and services to enable production ramp.
- Productization – Refine lab technology into integrated products addressing customer needs regarding usability, interfaces and form factors.
- Intellectual property (IP) – Quickly build patent portfolio around core innovations to block competition. Identify licensable IP for revenue.
Methodical execution conquering these elements transforms promising lab technologies into viable commercial thermal solutions.
Eco-Friendly Approaches in Electronic Heat Management
With sustainability crucial, various eco-friendly approaches are gaining prominence in electronics thermal management:
- Renewable cooling – Leveraging waste heat, geothermal, tidal or solar energy to power cooling systems. Reduces electricity usage.
- Natural refrigerants – Using naturally available CO2, ammonia, water or hydrocarbons instead of harmful synthetic refrigerants.
- Biodegradable materials – Thermal interface gels, encapsulants and flexible heaters made from organic substances that decompose safely.
- Water conservation – Closed-loop liquid cooling systems recycle water. Heat exchangers allow reuse of waste heat to reduce water needs.
- Waste heat harvesting – Capturing dissipated thermal energy for conversion into electricity using thermoelectric generators or Stirling engines.
- Recyclable materials – Designing for disassembly to recover and recycle metals, plastics and other materials after use instead of discarding.
- Renewable manufacturing – Utilizing sustainable processes like injection molding for plastics from plant starches to produce components.
- Energy efficiency – Careful design optimization, component selection, and control strategies minimize power consumption.

Adoption of green engineering principles enables thermal solutions that are environmentally sound over the entire product life cycle.
Reducing Carbon Footprint with Efficient Thermal Solutions
Thermal management contributes significantly to the carbon footprint of electronics hardware manufacturing and power usage. However, efficient thermal solutions can help reduce emissions:
- Energy optimization – More effective heating and cooling lowers electricity consumption resulting in lower greenhouse gas emissions.
- Waste heat utilization – Capturing and reusing waste heat avoids emissions from conventional heat generation.
- Renewable energy – Powering thermal management systems using solar, wind or tidal energy decreases grid reliance and emissions.
- Natural refrigerants – Eliminating synthetic fluorocarbon refrigerants with high global warming potential reduces direct greenhouse gas release.
- Recyclable materials – Designing for disassembly and material recovery reduces landfill waste and associated methane release.
- Sustainable manufacturing – Employing green processes like injection molding using plant-derived plastics decreases emissions from production.
- Durability – Reliable designs with long, maintenance-free operating life avoid emissions related to frequent repairs or replacements.
- Lean operations – Optimizing logistics and inventory decreases transportation emissions. Local sourcing lowers miles.
Innovating thermal solutions holistically applying sustainability principles will be pivotal for carbon footprint reduction as electronics usage grows exponentially.
Sustainability and Electronics: The Role of Heat Management
Effective thermal management underpins sustainability in electronics by enabling efficiency and reducing waste:
- Energy efficiency – Preventing overheating allows electronic systems to operate at optimal temperatures for the lowest power consumption.
- Product lifespan – Adequate temperature control protects electronics from premature failure thereby decreasing waste generation.
- Renewable integration – Efficient thermal systems allow coupling electronics with waste heat and solar energy for green operations.
- Water conservation – Closed-loop liquid cooling reduces water usage compared to continually evaporative air cooling.
- Recyclable materials – Recoverable metals, polymers, and composites used in thermal management components decrease landfill waste.
- Waste heat utilization – Heat recycling decreases net energy usage. Widely applicable with high heat fluxes from electronics.
- Reduced emissions – Lower power usage coupled with renewable energy integration and waste heat utilization diminishes greenhouse gas emissions.
- Eco-friendly design – The use of biodegradable organic materials and avoidance of harmful refrigerants reduces environmental impact.
Thermal innovation must align with sustainability objectives for environmentally responsible electronics manufacturing and operation over the product’s lifetime.
DIY Tips for Managing Heat in Home Electronics
Effective DIY cooling methods can protect home electronics from overheating:
- Elevation – Raise gadgets on feet or spacers to allow airflow underneath. Use wire racks instead of solid shelves.
- Orientation – Position units vertically instead of horizontally to improve natural convection. Avoid cramping heat vents.
- External fans – Use small USB/battery fans directed at hotspots to supplement internal fans.
- Under-volting – Reduce supply voltage to decrease heat generation, but test for stability.
- Heat sinks – Attach spare PC heat sinks using thermal epoxy or tape to hot components.
- Thermal Interface Material (TIM) – Apply heat sink compound between hot parts and chassis to enhance conduction.
- Ventilation – Ensure adequate clearance around electronics. Openings in enclosures can help airflow.
- Reflective insulation – Use foil backers to minimize heat transfer through walls and absorb solar radiation.
- Maintenance – Periodically clean dust from electronics and fans to maintain cooling efficiency.
Basic cooling best practices go a long way in protecting home electronics from thermal issues. Seek professional solutions for mission-critical systems.
Troubleshooting Common Heat Issues in Electronic Devices
Excessive heat can cause various issues in electronic devices. Troubleshooting approaches:
- Random crashes/shutdowns – Overheating components force safety shutdowns. Check for clogged vents, fans, and dried thermal paste.
- Throttling – Components automatically down-clock with rising temperature. Clean fans, elevate devices, and improve ventilation.
- Noise – Observe when fans get excessively loud indicating overworking to cool. Address hotspots.
- Artifacting – Thermal expansion of chip laminates can distort signals causing image artifacts. Improve heat sinking.
- Damage – Solder/components can melt, plastics warp, displays delaminate, etc. from temperatures beyond limits.
- Intermittent faults – Heat-induced propagation delays and racing conditions create intermittent glitches.
- High power usage – Components consume more power at higher temperatures, increasing heating further. Evaluate cooling.
- Reduced battery life – Heat accelerates battery discharge. Check for hot spots near battery.
A strategic thermal perspective helps troubleshoot and resolve common electronics issues exacerbated by overheating.
Maintaining Optimal Temperature in Electronic Systems
Achieving long-term thermal stability in electronic systems requires proactive maintenance:
- Monitoring temperatures – Use integrated sensors or IR thermography to identify hotspots and trends.
- Preventive cleaning – Regularly clear dust blocking vents and fans. Replace clogged air filters.
- Inspecting heat sinks – Check for damage or contamination blocking fins. Straighten bent fins.
- Replacing thermal paste – Periodic paste reapplication maintains optimal joint conductance. Avoid pumps out.
- Testing fan operation – Verify fans spin at rated speeds without excessive noise indicating wear.
- Evaluating insulation – Inspect for degradation allowing heat ingress/leakage. Fill gaps. Ensure integrity.
- Cleaning radiators/condensers – Flushing and brushing clears scales preventing proper working.
- Checking coolant health – Test quality and pH to sustain heat capacity and avoid blockages/corrosion.
- Validating clearances – Measure gap between components for adequate ventilation. Adjust space to improve airflow if needed.
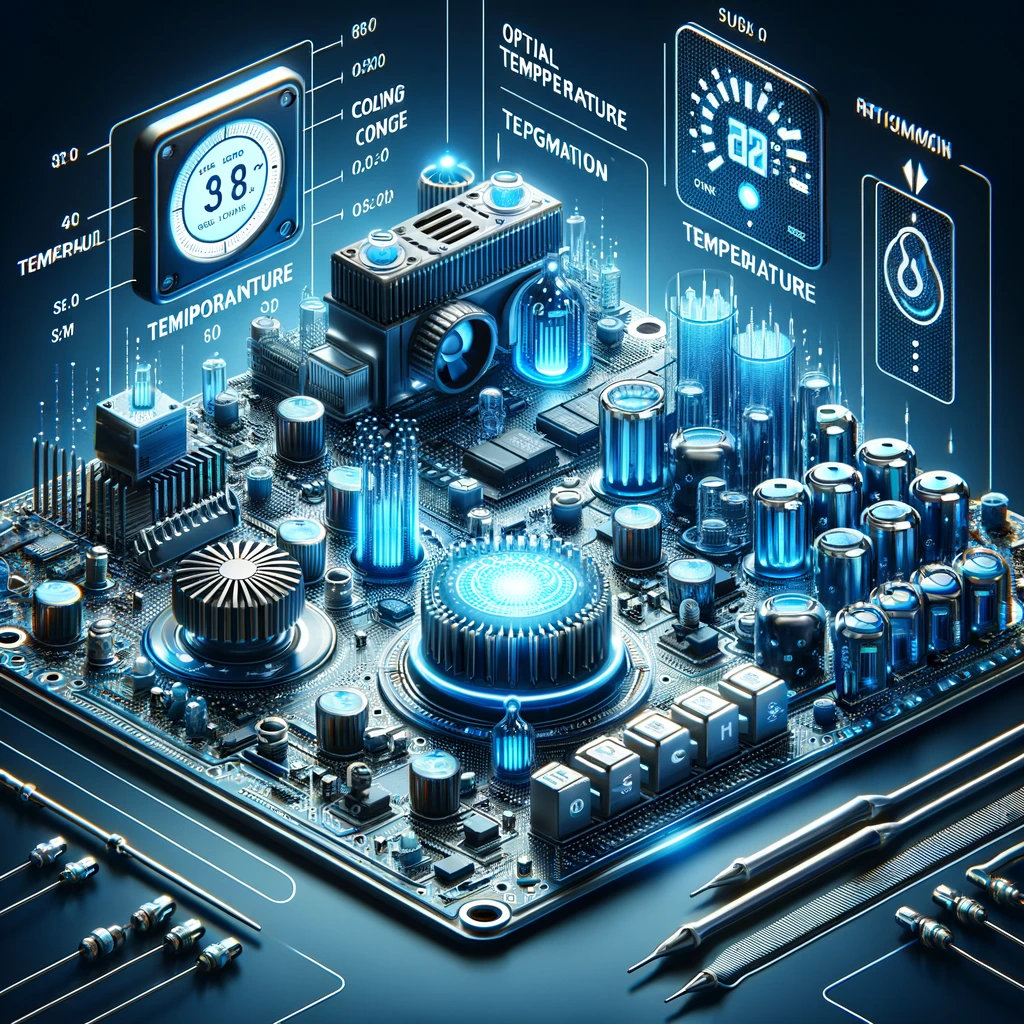
With proactive system health checks and part replacements, thermal management performance can be sustained long-term.
User-Centric Design: Heat Management for Comfort and Safety
Electronics thermal design must prioritize user comfort and safety:
- Heated surfaces in contact with users like enclosures and controls should maintain ~35°C to avoid discomfort or injury.
- Temperature sensors on gripping areas allow control systems to modulate heating levels automatically.
- Insulating hand-held portions thermally isolates hot internal electronics for comfortable handling.
- Heaters directed at palm contact regions prevent a cold feel. Useful for wearables or devices used outdoors.
- Breathable openings are tailored to ensure surface temperatures stay within safe limits for sustained skin contact.
- Fire-retardant, thermally resistant materials selected for enclosures prevent user risk.
- Warning labels indicate locations of high temperatures to avoid inadvertent contact during device operation and service.
- Rapid cooldown or thermal disconnect circuits are engaged when defaults are detected to prevent excessive exterior heat.
- Product testing validates safe human interaction over the expected range of user environments and handling conditions.
Adhering to safety standards and assessing user thermal comfort at the design stage ensures electronics remain safe for human interaction.
Enhancing User Experience through Efficient Thermal Solutions
Thoughtful thermal management engineering markedly improves the overall electronics user experience:
- Preventing overheating enables reliable uninterrupted operation without random shutdowns, crashes, or loss of data.
- Careful temperature control maintains optimal performance levels without throttling which slows workflows.
- Durable designs withstand years of wear without cooling efficacy deteriorating and causing premature failure.
- Quality thermal materials and interfaces reduce emitted noise from loud fans working excessively hard.
- Heated gripping areas enhance ergonomics by making handheld devices comfortable to hold in cold environments.
- Regulated outer surface temperatures prevent enclosures from feeling painfully hot or freezing cold during regular interaction.
- Display heaters reduce fogging and condensation issues for crisp, unobstructed viewing.
- Rugged thermal engineering sustains electronics usability in hot or frigid external environments.
- Sustainable manufacturing and operation give users peace of mind about ecological impact.
Innovative thermal solutions directly translate to positive user experiences further fueling electronics market growth.
Feedback Loops: User Input in Designing Thermal Management
User feedback provides crucial insights to refine thermal management designs:
- Surveys gauge subjective impressions of heat comfort, noise, and other factors affecting experience.
- Usage telemetry detects thermal fault events like system crashes indicating areas needing improvement.
- Community forums and social channels offer direct customer inputs on pain points.
- Beta testing on select users reveals real-world usage issues not detected in lab environments.
- Warranty and failure analysis uncovers common thermal failure modes in the field.
- Focus groups provide qualitative user perspectives on form factors, ergonomics, and noise levels.
- Social media listening identifies prevalent complaints about overheating or other thermal issues.
- Crowdsourced design input using consumer preferences to guide thermal engineering decisions.
Soliciting user experiences and feedback enables data-driven refinements in thermal management for superior real-world performance.
Navigating Compliance Issues in Thermal Management
Deploying thermal management solutions in electronics necessitates navigating complex compliance issues:
- Safety standards like IEC 62368-1 cover fire, electrical and mechanical hazards. Critical for consumer goods.
- EMC regulations like FCC Part 15 Class A/B electromagnetic emissions and immunity thresholds.
- Environmental regulations such as WEEE, RoHS, and REACH restrict hazardous materials usage and enhance recyclability.
- Agency approvals like UL, CSA, CE mandate stringent production quality and safety systems. Required by major OEM customers.
- Disclosure requirements like California SB-50 for restricted substances ensure responsible material sourcing.
- Certification testing – Rigorous testing by sanctioned labs to verify standards compliance before market introduction.
- Reporting obligations like EU EPREL product registration for energy efficiency ratings.
- Trade restrictions – Export controls on certain technology like thermal imaging cameras which have potential military applications.
Early regulatory analysis and compliance planning enables successfully bringing certified, standards-compliant thermal solutions to market.
Global Standards and Their Impact on Heater Design
International standards shape design choices in heaters for electronics:
- IEC 60335 – Specifies insulation, wiring, construction, temperature limits, combustibility requirements for consumer appliance safety.
- EN 60695 – Fire hazard testing protocols like glow wire tests at prescribed temperatures help select materials.
- IEC 60068 – Extreme environment testing procedures like rapid temperature transients guide design robustness.
- IEC 61000 – EMC emissions and immunity requirements like electrostatic dischargeresistance affect circuitry.
- MIL-STD-202 – Military-grade environmental stress tests for vibration, shock, acceleration. Help ruggedize solutions.
- CE marking – Mandatory conformance to health, safety and environmental standards for sale in the European Economic Area.
- RoHS – Restriction of Hazardous Substances directive bans lead, mercury, cadmium and more in electronics.
- ISO 14001 – Global standard for environmental management of operations and improving sustainability.
Designing to align with relevant standards upfront prevents costly rework later and enables global market access.
Safety Protocols in Electronic Heat Management
Safeguarding users necessitates rigorous safety protocols when developing electronic thermal solutions:
- Hazard analysis to identify risks – burns, fire, electrical shock, mechanical – and institute mitigations.
- Selecting thermally stable, flame-retardant insulating materials that meet flammability standards.
- Simulation and testing to ensure surface temperatures do not exceed defined limits for user contact.
- Evaluating electrical creepage/clearance rules are satisfied, especially for high-power systems.
- Mechanical and reliability testing for structural integrity to contain thermal loads safely. Prevents hazards.
- Warning labels indicating locations of high temperatures. Safety mechanisms like automatic controlled cooldown.
- Operator training on risks like servicing hot units, handling cryogenic liquids and proper protective gear.
- Developing careful standard operating procedures for managing fluids, gases and temperatures.
- Seeking certification by safety authorities after rigorous hazard review and testing instills confidence.
With diligent heat management protocols guided by standards, electronics can safely deliver functionality and performance.
Summing Up: The Future of Electronics Shaped by Advanced Thermal Management
In summary, thermal innovation determines the future capabilities of electronics. Advanced heating, cooling and thermal materials will be pivotal in overcoming miniaturization and efficiency hurdles. Compact flexible heaters, smart temperature control, liquid cooling and nanotechnologies promise transformative solutions to make electronics faster, more powerful, and sustainable. With thermal management intricately linked to industry growth, electronics will continue riding the wave of thermal design breakthroughs enabling performance milestones previously thought impossible. Exciting times lie ahead as researchers and engineers push boundaries in electronic thermal management.